Do you know how to make a pvc patch?
This article will tell you the function, classification, and production process of PVC patches
Table of Contents
- 1.What Are PVC Patches?
- 2.Features of PVC Patches
- 3.Raw Materials for PVC Production
- 4.PVC Manufacturing Tools (Partial Display)
- 5.Factory Mass Production Process for PVC Patches
1. What Are PVC ?
Polyvinyl chloride, abbreviated as PVC, is widely used in “soft rubber badges” (also called micro-injection molded emblems).
PVC patches are ubiquitous in daily life, though often overlooked. Examples include:
- Logo tags on sports shoes, slippers, bags, and outdoor apparel
- Luggage tags, keychains, phone charms, and other accessories
- Coasters, car mats, shoe soles, and even cycling gear
While some international clients refer to PVC patches as “rubber badges,” genuine rubber is rarely used in the label industry due to higher costs and technical limitations. PVC and silicone dominate this market.
Today, PVC remains the mainstream material for soft rubber labels thanks to its:
- Vibrant color options
- Cost-effectiveness (compared to silicone)
- Versatility in creating unique, colorful designs
2. Features of PVC Patches
- Material: Soft PVC (waterproof, wear-resistant, flexible)
- Techniques: Mold-cast with embossed (raised) or debossed (indented) effects
- Applications: Clothing/backpack badges, brand logos, military/tactical gear, fashion accessories
3. Raw Materials for PVC Production
- DINP oil (plasticizer)
- PVC powder (e.g., Korean or Hunan-sourced)
- Stabilizers
- Color pigments
- UV inhibitors
- Glow-in-the-dark powder
- Fragrance additives (optional)
4. PVC Manufacturing Tools (Partial Display)
(Note: This section would typically include images of tools like injection molds, mixing machines, etc.)
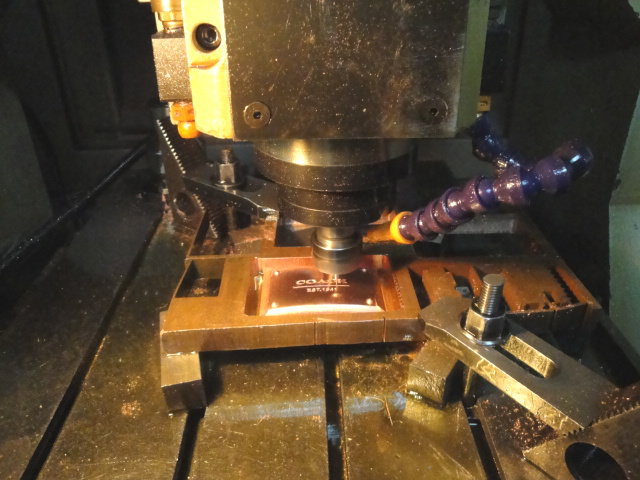
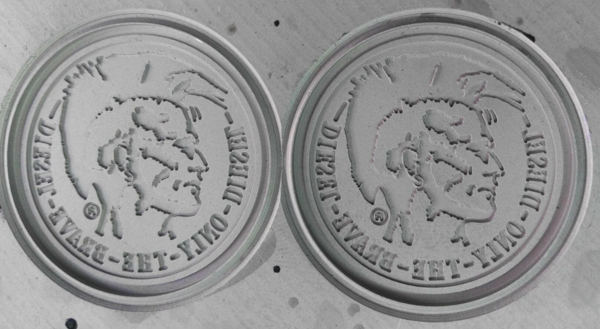
5. Factory Mass Production Process
Step 1: Design Preparation
- Vector files: Use Illustrator/CorelDRAW (AI/EPS formats) with clean outlines.
- Color separation: Specify Pantone codes (usually 1-3 colors).
- Special effects:
- 3D embossing: Layer designs for raised areas.
- Metallic/glow-in-the-dark: Requires specialty PVC compounds.
Step 2: Mold Creation
- Copper mold engraving: Custom-made based on design (cost: ¥500–2000, varies by complexity).
- Prototyping: Factory produces samples for approval.
Step 3: Production
- Material mixing: PVC base + plasticizers + colorants.
- Injection/compression molding: Molten PVC is pressed into molds under high pressure.
- Trimming & QC: Excess material removal and defect inspection.
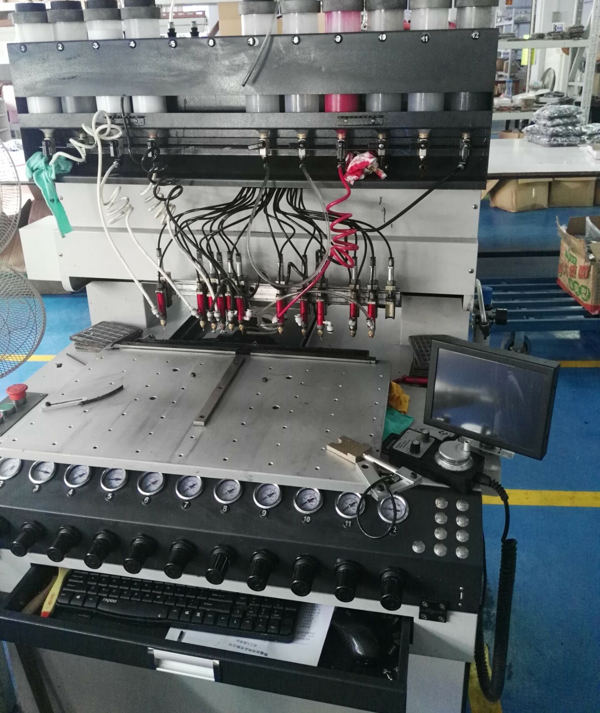
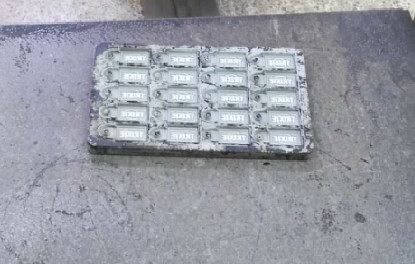
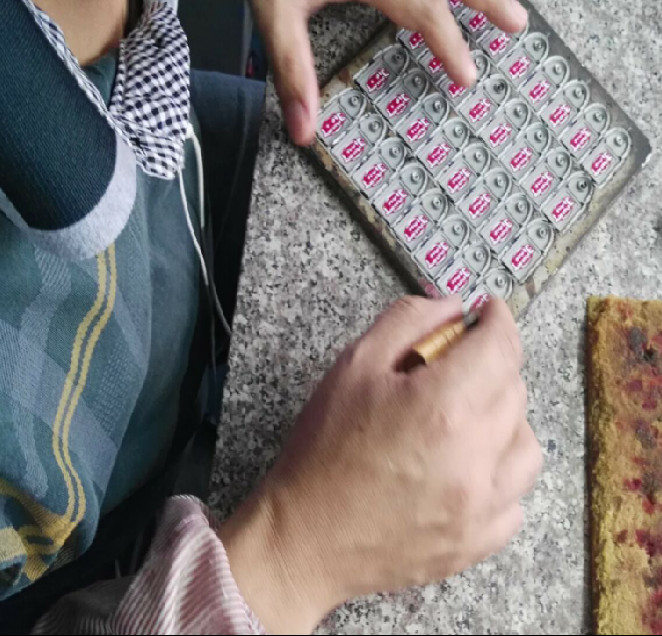
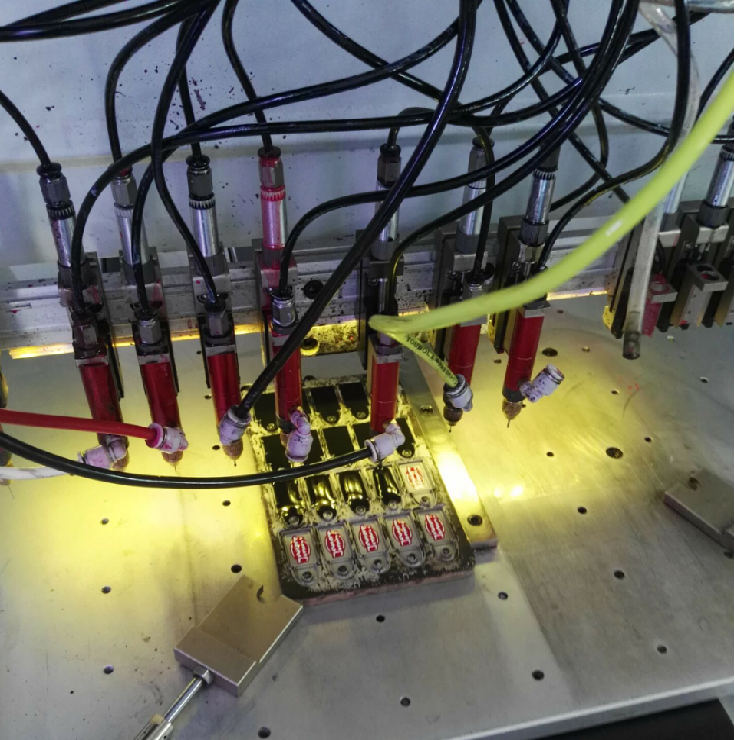
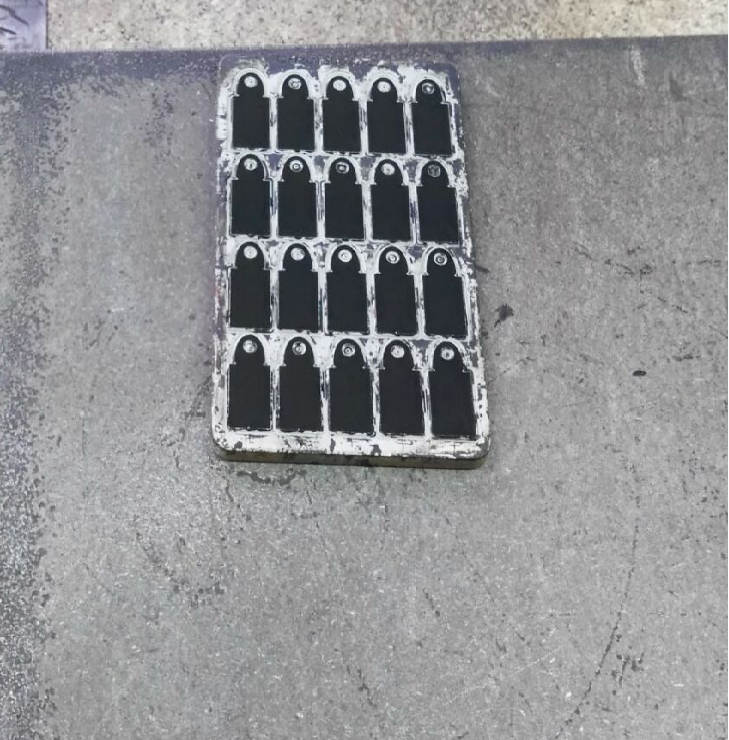
Step 4: Ordering Channels
Need factory recommendations or design optimization? Contact us at admin@web123.vip with your requirements (size/quantity/usage).
About Us: With 26 years of expertise in PVC patch manufacturing, we guarantee prompt responses and professional solutions.